Vacuum Pump Solutions
The following posts highlight solutions we have offered our customers for common issues.
Leybold TRIVAC Rotary Vane Pumps: Gas Ballast Operation
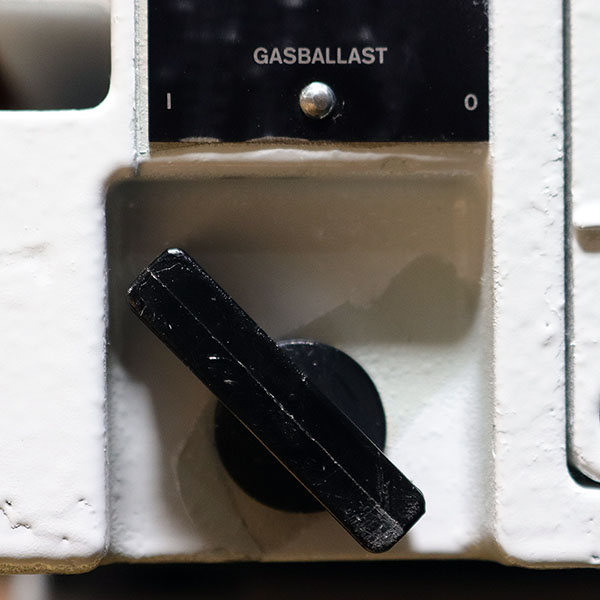
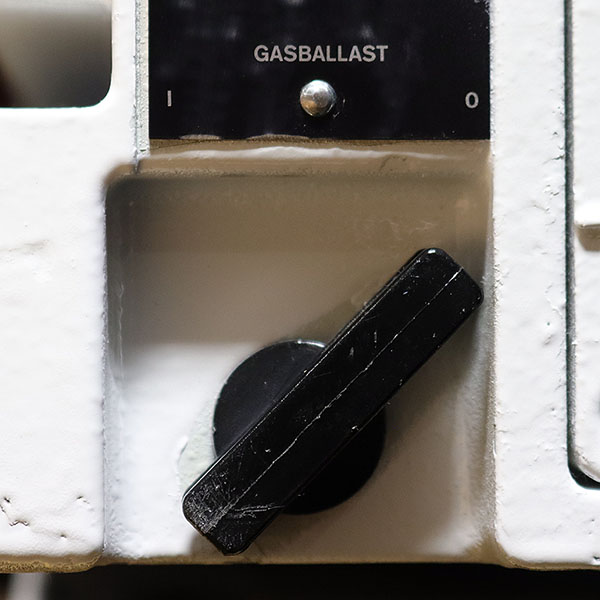
The gas ballast valve in the counterclockwise position (pointing left to 1) is open and ON. Clockwise position (pointing right to 0) is closed and OFF.
Pros & Cons of GV Dry Pumps vs Piston Pumps
Cons: Higher acquisition cost, nitrogen purge required (air is OK in a clean processes) Pros: Lower overall cost of ownership, longer mean time between repair, superior particulate and water vapor handling, no oil back streaming, narrower footprint, blower mounted directly above pump
Oil contamination
Aerospace customer noticed that a cryopump installed on a large vacuum chamber would not pump down below 10-5 range. Additionally he found oil contaminants on the 80K array. While there is oil used in the cryogenic system in the compressor and it can contaminate the helium circuit, this oil can not physically reach the vacuum vessel. Large “wet” pumps such as piston pumps are major contributors of oil back streaming into the vacuum chamber. This is due both to design and the large size of the pump’s inlet when compared smaller sized inlets of rotary vane pumps. In this specific case, the customer was using a large Piston pump to provide rough vacuum to his chamber at about 15 Microns. PTB’s recommendation: Increase the roughing to 50 microns from 15 (whatever rough pump is used) and do not let the rough pump, rough for any length of time to lower pressure. However for a long term solution, consider a different type of rough pump. A dry pump would be optimal, but a rotary vane would be better than a piston pump for this application. If the Piston pump is the only option, then PTB recommends an inlet oil trap, these traps are typically available from the OEM.
Pfeiffer Adixen Alcatel 2021i Rotary Vane Pump: Poor base pressure, see photo
The problem was not duplicated. Oil was put into the pump and the pump went on tested run over 24 hours. It was pulling 2 mTorr and using 3.8 amps with GB off. However, the oil was drained after testing (to prepare for shipping) and a significant amount of water / liquid was noticed in the drained oil. It is recommended, based on the residual liquid that came with the pump, that the customer should change the oil more frequently.
Welch DuoSeal 1402 Rotary Vane Pump: Belt guard missing, unit leaking oil
Regarding the oil leak; the problem was not duplicated. There was some oil seen dripping from the exhaust port; this was re-condensed oil vapor exiting from the exhaust. This vapor was caused by the gas ballast being open. Once the gas ballast was closed, the pump was tested for 72+ hours and no oil (leak or condensation) was seen.
Leybold D65BCS Rotary Vane Pump: Pump was seized
The problem was duplicated. The pump was seized. Upon tear down, small amounts of debris was found on the ASB valve metal to metal contact / grinding was seen between the first stage rotor and the front plate. This was stoned smooth; pump reassembled; tested and operated satisfactorily (2 mTorr @ 2.7 amps). It is unclear what caused this grinding. One possibility is particulate in the process, which can start the destructive grinding. Customer should investigate whether any material is getting into the pump and / or if a particulate filter would be beneficial.
Stokes 212H-11 Piston Pump: Seal leak
The problem was duplicated. There was a seal leak. The oil case was opened and large amounts of dark thick paste was found in the oil. The paste appears to be metal fines mixed with oil. The cause of the seal leak was metal fines forming a grinding paste which eventually wore thru the seal. A second more serious issue was discovered however, also caused by the grinding paste. The Hinge bar and its bore had too much play. This gap between the bar and the bore appears to have been widened by this grinding paste. This will require a new seal, new hinge bar and the pump lower will have to be sent out for re-boring. This problem is process related. To avoid future similar problems, it is recommended that the particulate filter for this pump should be reviewed. The mesh / micron size verified for the material in the process gasses. Until the particulate issue has been solved, the maintenance interval for oil change and filter clean out should also be decreased.
Busch RA0100.E5Z6 Rotary Vane Pump: The problem was duplicated - the pump was seized, see photos
The color of the oil thru the sight glass was dark clay. The oil was drained. The oil was completely contaminated. A combination of water and thick sludge. The view inside both inlet and outlet ports should that both were covered in the thickened sludge as well. The internal pump parts seen were covered in rust. The contaminated oil thickened, lost it's lubricating qualities causing the vanes to stick (not retract) and hence the pump seized. This failure is process related. A couple of considerations for improving the pumps performance are:
- Use of gas ballast during operation, causing the pump to run hotter and help prevent condensable forming in the oil
- Not turning the pump off after a process run for the same reason as above
- Changing the oil frequently and review of maintenance schedule
- Oil sight glass should be used not only monitor the amount of oil but to monitor the oil color as well. Any significant color changes should dictate an oil change.
Leybold D60AC Rotary Vane Pump: Seal leak, see photo
There was a leak thru the seal on this pump. The residue (still on the pump) indicates that oil was dirty (dark brown) and had particulate in it. It's the particulate in the oil that will grind thru a seal. This particulate has compromised the pump shaft, as well, by material grinding a ring in / through it. Even if the residue wasn't seen; grooves in the shaft (seals) indicate dirty oil (within such a short period). As a courtesy we have replaced the seal (using a spacer to place the seal above the groove in the shaft), and have tested the unit for 24 hours with success. No leaks - pulling a vacuum of < 1 mTorr. Without a full rebuild this, I believe, is the best scenario. Obviously, given the state of the shaft, the next rebuild will require (at a minimum) replacing the shaft.
Leybold D65B Rotary Vane Pump: Making noise and losing pumping ability, see photos
The color of the oil thru the sight glass was dark brown / black. A visual inspection thru the inlet port showed that it was covered bronze colored particulate; thru the exhaust port black sludge could be seen covering the pumping module. The black thickened oil was drain and collected in case customer would like to analyze the containments. It seems as if the customer process is particulate laden this particulate contaminated oil causing lack of lubrication and hence pumping ability. This pump will need to be rebuilt. This failure is process related. A review should be undertaken to determine the last oil change undertaken on this pump to develop a process specific maintenance schedule. The oil sight glass as well, should be used not only to monitor the amount of oil but to monitor it's color as well. Any significant color changes should dictate an oil change.
Pfeiffer Adixen Alcatel 2021i Rotary Vane Pump: Poor base pressure, spewing oil
The problem was not duplicated. The pump came in drained of oil. However, the residual oil smelt similar to gear oil, not vacuum pump oil. Inland 19 oil was poured in and out of the pump twice, in order to flush out any residue from the oil case. Once clean oil was put in the pump, it was tested over the weekend and performed satisfactorily: Base pressure of 6 mTorr with no oil leaks. This Inland 19 oil used to flush the pump (with residue) has been saved in case the customer would like to analyze it. It seems as if the wrong oil was used in this pump. The customer should confirm that the proper oil is being used and / or correct if not. At this point, with no problems found, this pump is ready to be shipped back.
Leybold D60AC Rotary Vane Pump: The problem was duplicated - there was a leak in the front seal, see photos
The residue oil of this leak was brown and contained fine particulate. From the color of the oil in the pump and residue / grit from the seal leak, that the contaminated oil with this fine particulate, ground its way through the seal causing the leak. This is a maintenance issue - specifically an oil change scheduling issue. As a courtesy, we can replace this seal free of charge and send the pump back; however, I would recommend a complete rebuild of this pump.